Covering the Fokker DR1
- Robareeno
- Nov 8, 2021
- 7 min read
Updated: Aug 26, 2023
This is the part of construction that scares new builders off. I promise you it is not hard. Let me help take away the mystery.
Prior to the design of this airplane I was mostly happy with using a simple over the counter iron on covering. In fact check out my link and instructions previously posted for doing this here: This is certainly an acceptable solution but read on as I want to share the lightest weight and in my opinion the most beautiful covering solution I have found so far.
The best method in my opinion is Iron on Silk covering. With this method you are literally making your own iron on covering from an incredibly lightweight natural material. Because it is a fabric and not a plastic sheet it gracefully wraps and bends around corners. It stretches, and naturally shrinks in the covering process to a tight drum. At the end you have a very authentic looking finish that is far easier than expected, and will likely land your model in a fine antique store in 50 years assuming you don't auger it in somehow long before that. Thank you happy RC Dude for the awesome informative post.
Oh, you can also forget about using expensive, hard to find, stinky, and toxic Aero gloss Dope chemicals as well because this method uses water based single part polyurethane available at any hardware store for cheap.
The following picture is the result of my first effort on the lower wing. This was just after letting the first coat of of brushed on polyurethane completely air dry.
So where to get this fancy stuff? Thai silks. You need to purchase Habotai 5mm cloth. Here is the link: It will take about 2 yards of the fabric to cover the plane if you get it right the first time. Don't stress though, order an additional yard for the learning curve. It's quick but you may wish to re do some of your first attempts. Then again, you may not be as OCD as I am. As for the polyurethane I used Rustoleum Parks pro finisher water based polyurethane for floors. Other brands will probably work just fine I just find this product to be my favorite.

Making the iron on covering:
This is a quick description as I encourage you to watch the videos above but the basic process is this:
Using a large mirror or plate of glass, span out a sheet of silk over the glass, make sure it fits with room to spare. Using a short nap paint roller wet the silk down. Gently pull the silk out from the center to the edges, removing any bumps and trapped air. Then gently blot the silk with an absorbent towel to remove excess water. You only want it slightly damp.
using a short nap roller begin in the center and roll a coat of the poly into the weave of the fabric. Go over it repeatedly to stipple it and ensure complete even coverage.
using a typical window cleaning squeegee, gently squeegee over the to of the silk, again from the center out. I don't use any more pressure than the weight of the squeegee. You are simply trying to remove the excess that did not get stippled down into the fabric.
Once you are happy that you have a completely even and smooth surface leave it to dry for a couple hours. Once dry, the covering will peel from the glass quite easily. Notice that there will be a mat side, and a shiny side adjacent to the glass.
Brush your model at any location that will be in contact with the covering with a coat of poly and let it dry.
Covering the Model:
measure out your new covering in much the same way you would with any iron on covering. Be sure to leave enough over any corners to give you room to tug and pull as you work the next step.
Re wet the silk piece that you will be applying and lay it shiny side down on the model. This is an iron on covering. The iron will soften the poly and make it adhere to the poly that you painted on the frame. It is very important to note that the iron will not shrink your covering. Drying does that a bit. Mostly you need to get the fabric taught while it is still damp though. It will not shrink nearly as much as plastic covering. Work the peace carefully and bond the seams with the iron, attempting to pull the fabric taught as you go. Make sure that you keep the silk damp. The silk will shrink as it dries. If a part is taking a bit of time, it will likely begin to dry on you so re mist the part with water as you are working to keep it as stretchy as possible. The iron will remove the moisture where you are sealing. The fabric stretches beautifully around corners. Continue working with it until you get a good tight covering while damp. Note that you can apply your covering iron to any area where you need to re soften the bond if you need to re pull on an area to remove a wrinkle. Once you are satisfied with your result, cleanly cut away any excess and ensure that the seams are thoroughly bonded down with the iron. Then proceed to the next panel in your covering sequence allowing the part to dry completely.
Thin the poly down just a small bit to the consistency of half and half creamer. I also use a very light, round bristle artist brush. Gently brush a coat of the poly into the fabric and continue brushing wet areas until you have the silk evenly coated. You can dry brush overly wet areas to wick the poly back up and apply it elsewhere. Also ensure that you have a good coat at all your seams. Make sure that you do this on all sides of a part at once so that everything tightens evenly as it dries. you will probably see wrinkles where you had none appear before. They will disappear again when dry. Let the part dry thoroughly.
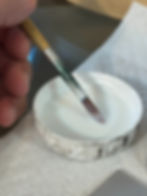
Rinse and repeat. These are very thin coats but you need to fully impregnate the fabric leaving no dry weave exposed. A dry weave will turn in to pinholes in the finished painted surface. Now is the easiest time to eliminate them.
Troubleshooting: With the second coat you may get some unexpected wrinkles that stubbornly don't go away. Here is a tip to correct it. Once the part is absolutely and thoroughly dry, run the part under hot tap water briefly on all sides, then let the part dry again. This trick tends to even out the stretching and allows the fabric to re tighten. The warm water also plays a role in this. This is an advantage of a 3D printed model, I'd never attempt this with balsa wood.
Painting:
It’s not really needed. The model is actually quite beautiful at this point but its clearly the wrong color So let’s proceed. Any good painter will say that the secret to a beautiful paint job is in the prep work. Let’s back up to that point. Have you sealed the fabric with poly? At least twice? While you don’t want to cake on any finish, you do need to ensure that you do not have a dry weave in the fabric. This is where tiny pinholes can still exist. They will become glaringly apparent as soon as you shoot your first primer on the fabric. See pic below. This is an example of what it should not look like. This will not happen if you adequately seal the fabric to begin with. Unfortunately it is almost impossible to see them until the first primer goes on.
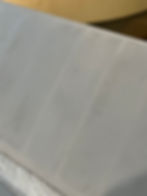
It may be tempting at this point to shoot another coat of primer, don’t do it. It is amazing how it will build up everywhere but in these areas. They are quite stubborn. Go back to the poly and brush apply a thin coat of poly.
Holding the brush toward the end, I gently work the sealant in to the fabric and then continue to smooth any excess on to the next area. This sealant shrinks considerably when it dries so you will be hard pressed to find any brush marks at all. Now back to the primer. Before shooting anymore use a small piece of 350 grit sandpaper and lightly run it over any areas that have imperfections. You may find a lot of tiny hairs at the seams or globs that you didn’t see before. They will quickly remove. If you want to completely eliminate a seam edge this is the time to do it. You will be surprised at how much you can easily remove. Only stop once the color of the primer is gone from the fabric. The fabric is very tough but you can eventually go through it if not careful. Gently use a tack cloth to remove any dust or sanding residue. You are now ready for the next primer coat. All the primer coats should be light to medium. Probably more light than medium. Heavy coats don’t fix anything, and only add weight to your model. If done right, your second coat will look greatly improved, and likely all that is needed before shooting color.
Shooting the color:
Again, proper preparation is the key. Look over the model for flaws in the primer. Once you are satisfied, carefully clean the surface with a tack cloth. It is important to keep the area you are painting dust free. This includes things that may fall into the paint, (like bugs if you are doing this outside.) I always give myself enough area around the model part to test shoot a bit of paint as a test prior to shooting the model. Then I use fluid motions to apply an even light coat on the surface. Never stop motion on the model part while you are still spraying.

Rattle can paint:
All you air brush guys can skip this part but I just needed to comment here that its important to read the instructions on maximum times between coats. It’s easy to lay a part like a wing down flat and shoot a beautiful finish on it. Then wait 3 or four hours, flip it over and shoot the bottom, only to find a terrible reaction, (called busting) where the solvent in the wet paint penetrated in to the freshly drying, and not sufficiently hardened paint shot previously. That paint will expand, and can wrinkle up terribly. The key to avoid this is to stay within the recoat time, or be far beyond it say 48 hours or more.
That is it for covering! Check the main blog here for the next steps. Feel free to reach out to us with any questions. We will attempt to clarify the construction blog including your input as much as possible.